What the U.S. Can Learn from Europe's Construction Ecosystems
This May, Terner Labs brought our Builders Lab cohort - B.PUBLIC Prefab, MODS PDX, Cloud Apartments, Villa Homes, Cycle Retrotech, and Hydronic Shell - on an international trip to Sweden and the United Kingdom.
The Builders Lab is an accelerator program which works with emerging leaders in architecture, engineering, construction and hardware manufacturing to scale effective and sustainable methods of housing delivery across the U.S.
The aim of this trip was to expose cohort companies to more mature ecosystems of industrialized or “modern methods” of construction (IC or MMC), generating actionable insights across a range of perspectives to inform further innovation here in the United States. We visited:
Housing factories: Derome and Vida (construction firms using wood-based building systems to deliver housing)
Knowledge-building coalitions: LFM 30, BE-ST (BE-ST), Edinburgh Home Demonstrator (EHD), Växjö Linnaeus Science Park, Energiesprong UK (organizations bringing together private and public actors to exchange best practices and advance sustainability, technical research and development)
Developers: OBOS and MKB (large developers using varying degrees of prefabrication, one producing housing to sell to homeowners and the other producing build-to-rent publicly-owned housing
Architects: Wingardhs and Arkitektbolaget (firms with a high commitment to sustainability and the use of prefabricated systems)
Material and equipment suppliers: Södra and James Jones & Sons (world-class sawmills producing wood-based construction materials) and Randek (global provider of prefabrication production systems for factories)
Key insights for U.S. innovators
1. Vertical integration is a powerful strategy, but is not the only way to succeed.
Some of the companies we visited demonstrate the success that can be achieved through vertical integration. Derome, a third-generation, family-owned company (and one of the largest home builders in Sweden) incorporates traditionally fragmented roles such as development, manufacturing, and general contracting into one organization.
Other companies, such as James Jones & Sons in Scotland, were not vertically integrated, instead relying on key long-term partners to complete the housing value chain. They sell products to an array of industries beyond construction (for example, pallets for materials handling). This diversification across markets and industries insulates them from isolated market downturns.
Reflecting on the differences, one of our cohort members put it this way: “Vertical integration is an outcome of success within a specified sector, rather than an input to company success.”
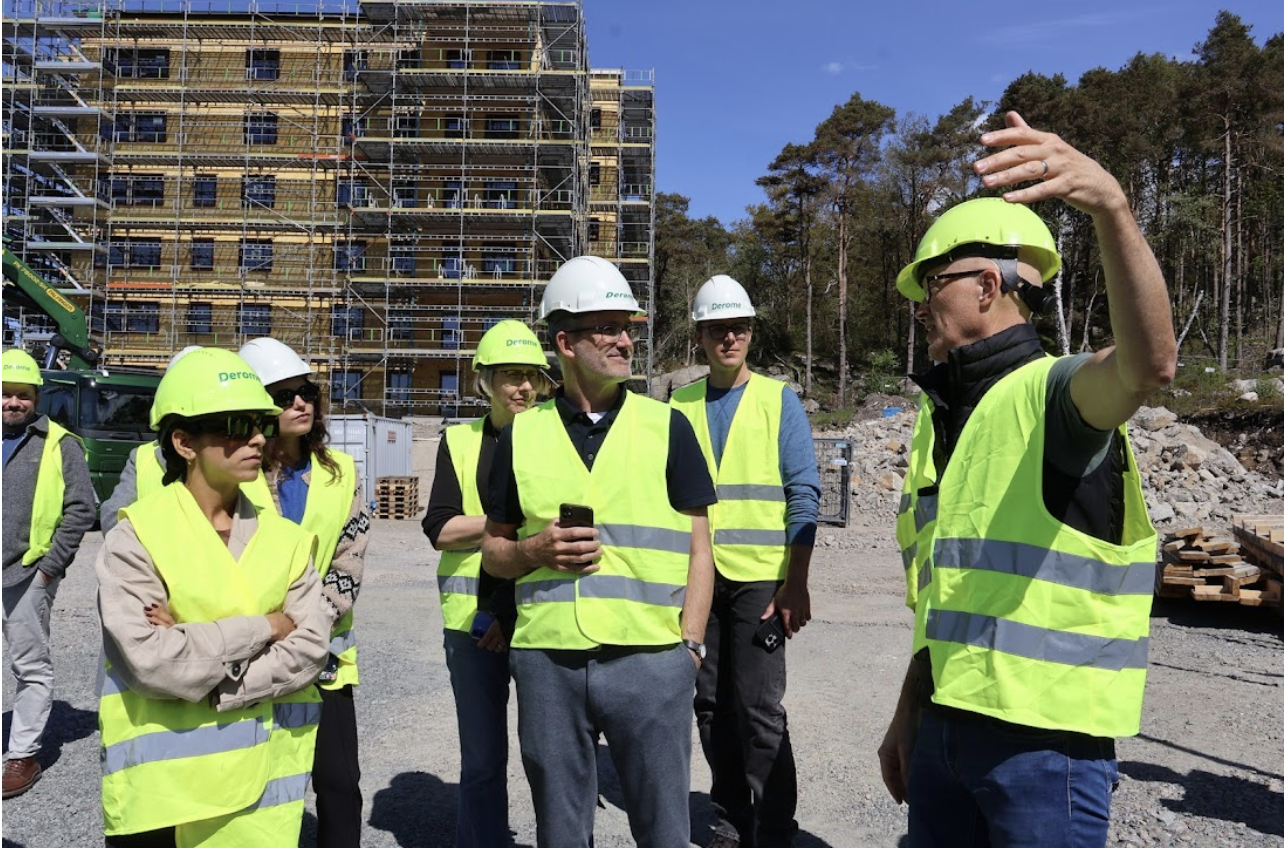
2. The building method should follow the product.
The successful companies and projects we saw first determined what they needed to build and then asked how.
During our visits, we observed that panelized systems were often used for single-family homes and build-to-sell models because they allow for more bespoke designs and flexible floor plans. Volumetric modular building systems, on the other hand, were more commonly used for multifamily and build-to-rent projects where speed and cost metrics were prioritized over design customization. Panelized and volumetric modular building systems can (and should) coexist as viable solutions for specific markets and housing types.
In pointing out the importance of aligning method with product, an industry veteran in Sweden emphasized that companies should “not be afraid to specialize”. In practice, this might mean specializing when determining customer segments, the corresponding housing technologies, and, following that, the most appropriate construction methods.
3. Regional context shapes how IC/MMC businesses develop and operate.
Regional differences in policy, resources, customer preference, demographics and other factors lead to variation in companies’ business models, building materials, and success metrics.
For example, in the UK, the government defines MMC as a wide spectrum of innovative construction techniques, ranging from improvements to onsite processes to the use of offsite methods like prefabricated panels or volumetric modules. This spectrum of techniques included within the MMC umbrella allows significant variation in the adoption of MMC while providing a framework to encourage incremental, industry-wide improvement.
To complement the broad terminology, the UK government created a “pre-manufactured value” (PMV) metric to specifically quantify the proportion of hard costs held by off-site component production. This allows policymakers and industry actors to quantify the breadth and depth of off-site construction methods' market penetration as an "apples-to-apples" comparison instead of only tracking discrete categories (such as whether or not a project is using volumetric modular units).
In Sweden, a different set of regional factors has shaped the adoption of new construction techniques. After changes were made to national building codes in the mid 1990s allowing wood-based building systems for multi-story buildings, adoption of IC/MMC grew alongside the uptake of wood in construction writ large. An expansive focus on environmental sustainability in recent years has added further momentum to wood-based construction, as it tends to offer lower embodied carbon than steel or concrete. These factors partially explain why many IC/MMC companies in Sweden choose wood-based methods and place particular emphasis on sustainability metrics as a key competitive advantage.
In the U.S., a high level of regional diversity in policy, material availability, building codes, and customer preference will inevitably lead to differences in the growth of IC/MMC by region. Policymakers should be mindful of the incentives and embedded assumptions behind regulation intended to improve the building industry, and companies should tailor their products, methods, and business models to regional factors.
4. Companies can and should align shared value (to external partners and the environment) with shareholder value (clients and investors).
A common thread in both Sweden and Scotland was the prioritization of long-term goals as a critical part of good and durable business practice.
Though cost is a priority, the companies we talked with also highly value other criteria for pursuing innovation, such as the capacity of long-term supply chain partners and alignment with climate goals.
Many of the stakeholders we engaged with integrate core sustainability metrics (such as energy efficiency or embodied carbon) into decision making; not as nice-to-have marketing features or regulatory requirements, but as essential elements for maintaining relevance and ensuring long-term competitiveness in the marketplace.
However, these are not viewed as cost-drivers (at least over the long-term). “BATNEC: Best Available Technology Not Driving Excessive Cost” is a Swedish aphorism which affirms that innovations in building sustainability might come at a slightly higher cost, but as long as it’s not excessive, innovation is not at odds with project-level feasibility or the creation of shared value.
5. Innovation and improvement take time and effort.
Adoption of IC/MMC did not happen overnight in Sweden or Scotland, nor is it complete. In both countries, this process has been characterized by a commitment to continuous improvement by individual companies and multi-stakeholder partnerships.
Collaboratives like Växjö Linnaeus Science Park, BE-ST, and EHD support pilot projects building upon previous innovations. Innovation happens within companies, too - for example, one company we visited embeds improvements into their internal workflows by requiring each team to report at least 75 improvements each year. These can range from minor improvements like simplifying a customer intake form to more significant undertakings like the adoption of a new automated assembly system.
Metrics that quantify the benefits of adopting innovation can be a powerful tool. For example, the LFM30 regional initiative in Sweden has signed more than 200 members up for voluntary compliance with more stringent sustainability goals than those required by law. The EHD initiative in Scotland used key metrics demonstrating lower long-term utility and maintenance costs to convince six regional governing bodies to support the use of panelized building systems for new housing.
Models of success
In Scotland, BE-ST offers an inspiring model which could translate well to several U.S. regions. This initiative facilitates collaboration between industry stakeholders which might otherwise perceive joint R&D as a competitive disadvantage and offers hands-on experience for workforce trainees. Government funding served as an important catalyst for this industry-led, academia-anchored collaboration.
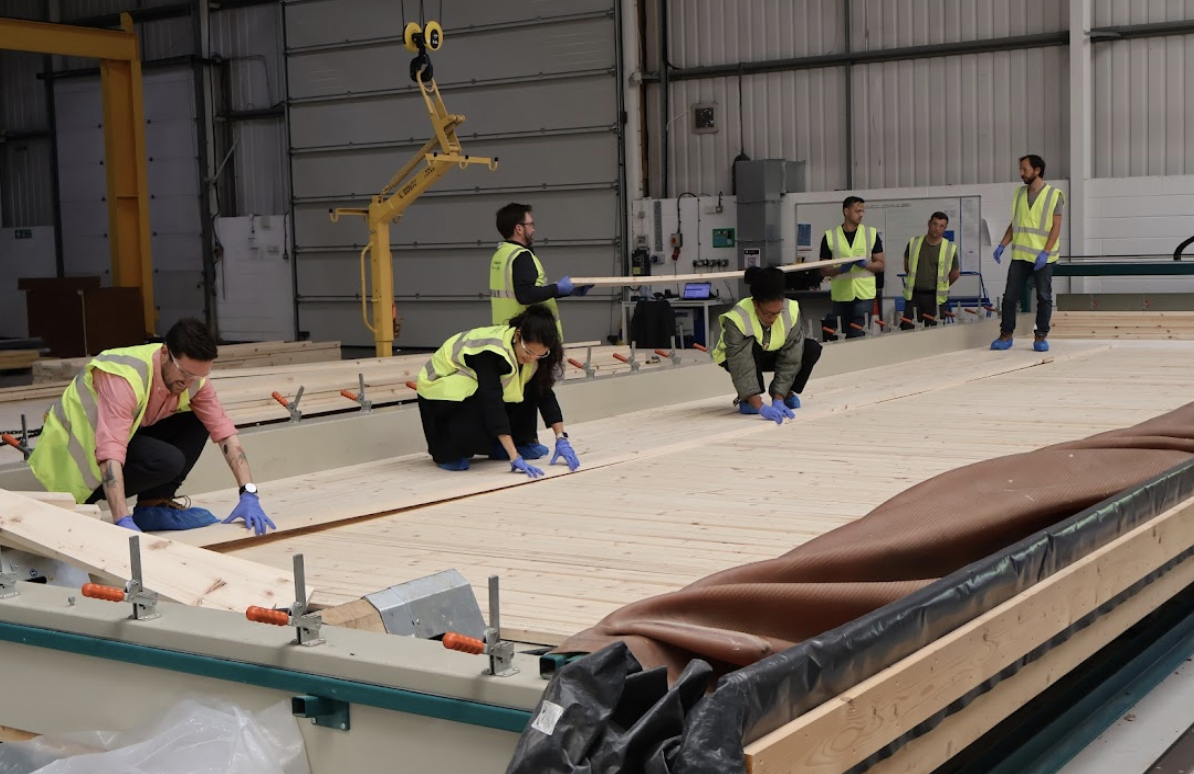
Scotland and the U.S. experience similar construction workforce challenges, including labor shortages and a historic perception of careers in the construction trades as less desirable.
Edinburgh Napier University and their Center for Net Zero High Density Buildings is leading an initiative to invert this narrative by equipping the IC/MMC workforce with specialized technical skills that help them become key contributors to climate-impact work. This type of initiative could be replicated in the U.S. to boost interest in construction among young people.
Thank you
It’s difficult to capture the richness of this experience in one piece, but we hope this summary offers some inspiration for innovators in the United States. We’re still energized by the fantastic memories and valuable insights gained from our trip, and want to offer heartfelt thanks to our wonderful hosts across Sweden, Scotland, and England for generously sharing their time and expertise with us. We're also deeply grateful to our strategic partners, whose financial and programmatic support has made the Builders Lab possible.
If you’re interested in learning more about what we saw during the trip, join us for a deeper dive via an upcoming webinar on July 9. Register here.